- Before
- 成形機から出てきたワークを手作業で治具にセットし、組立のみ機械が行う半自動機を使用していた。
- After
- コンベアで流れてくる成形品を、2台のロボットでつかみ、組み立て、シールを貼り、NG品の排出を行う全自動機を導入。完全自動化となり、作業員1名を削減。
ワークの種類 | 樹脂成型品2種 |
---|---|
納入先 | 樹脂成型品メーカー |
工程・用途 | 組立/搬送/ラベル貼り/ラベル検査/3Dピッキング |
プロダクト | 3Dビジョン・産業用ロボットを使用した自動化装置 |
課題
24時間稼働する工場であるため、夜間の作業員確保が困難だった。
半自動機は手を挟む危険のある構造になっていた。
ご提案
ロボット2台で部品の組立、ラベル貼り、ラベル検査作業を自動化。
人による手作業をすべて省略可能に。
完全自動化により、半自動機使用時に起こりうる労災も防止。
装置の動き
①樹脂成型機からガントリーで取り出されたワークが、コンベアで運ばれてくる。
②3D カメラでワークの位置を捕捉し、ロボット1がピッキングする。
③ロボット1がワークAは裏向き、ワークBは表向きになるよう、溶着機にセットする。
④溶着機でワークAとワークBを溶着。
⑤組立後のワークへ、ロボット2がバーコードシールを貼る。
⑥バーコードの位置をカメラで検査する。
⑦ロボット2でOK品を、排出コンベアに25段ずつ積み上げる。
NG品は後ろ側に排出する。
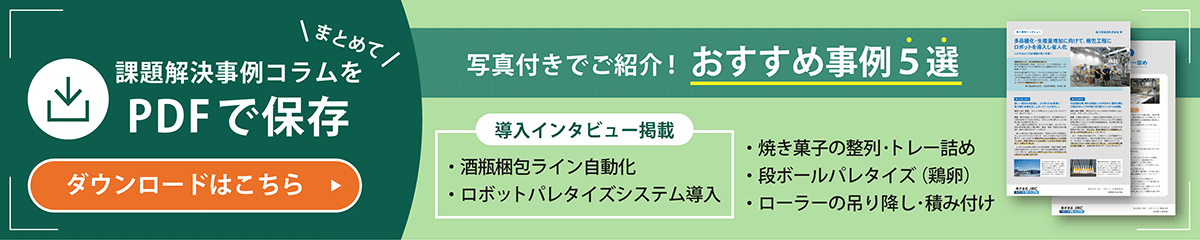