- Before
- 作業員2名で、ローラの芯が歪んでいる方向からハンマーで叩き、歪みを修正していた。
- After
- まず大型の装置を導入し、全サイズのローラの歪取り作業を自動化することで作業員1名削減。
その後小型の装置を導入し、軽くて小さいローラの歪取り作業を更に効率化。作業時間を5分から1分程度に削減。
ワークの種類 | ローラ 最大500kg(大型装置)/ 最大100kg(小型装置) |
---|---|
納入先 | 株式会社JRC 九州工場 |
工程・用途 | ローラを溶接後、駆動側の芯の歪みが0.1 ㎜以下になるよう 修正 |
プロダクト | 自動化装置(大型装置)/ 半自動化装置(小型装置) |
ハンマーで叩いて歪を修正する作業は、労災の危険のある重労働だった。
どの程度の力で叩くかは手の感覚で覚える物で、ノウハウが属人化していた。
1号機導入後作業は楽になったものの、大きいサイズのローラに合わせて設計された装置では、小型のローラの作業の際にも長い時間がかかっていた。
装置が歪を検出しプレスして修正することで、人が行う作業はローラの設置と装置の操作
のみになり、作業員の削減に加え作業の負担を軽減。
1号機には大きいローラの太い芯を修正できるよう、パワーの大きい油圧プレスを採用。
小型のローラ専用の2号機には、速度の速いサーボプレスを採用することでタクトタイムを
短縮。
1号機は歪み測定を全自動で行うため、測定に時間がかかる。2号機は手動でローラを回転させ測定する方式に変更することで、目視で測定不要箇所を省く。
■1号機
①ローラの情報を入力。
②ホイストを使用し、ローラを設置。
③装置が自動で歪み箇所と歪み具合を測定。
④測定結果を元に、押し込み量を入力。
⑤油圧プレスで歪み箇所を押して修正。
■2号機
①チェーンブロックを使用し、ローラを設置。
②手動でローラを回転させながら、
歪箇所と歪み具合を測定。
③測定結果にを元に、押し込み量を入力。
④サーボプレスで歪み箇所を押して修正。
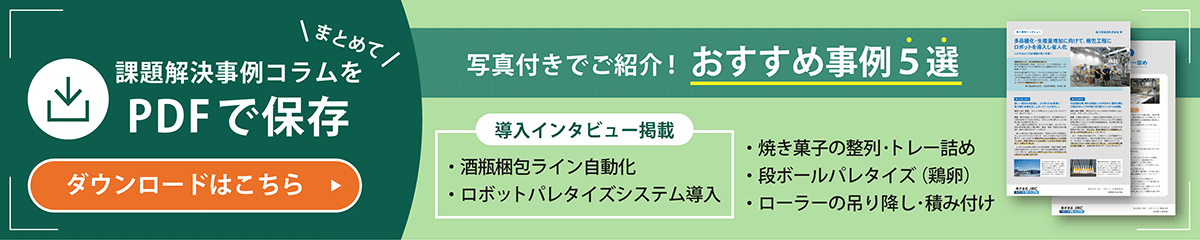